» Veranstaltungen
» Navigation
» über uns
|
» Registrierung
Liebe Mitleserinnen, Mitleser, Foristinnen und Foristen,
wer sich von Euch in letzter Zeit mit dem Gedanken getragen hat, Mitglied unseres wunderbaren IGDH-Forums zu werden und die vorher an dieser Stelle beschriebene Prozedur dafür auf sich genommen hat, musste oftmals enttäuscht feststellen, dass von unserer Seite keine angemessene Reaktion erfolgte.
Dafür entschuldige ich mich im Namen des Vereins!
Es gibt massive technische Probleme mit der veralteten und mittlerweile sehr wackeligen Foren-Software und die Freischaltung neuer User ist deshalb momentan nicht mit angemessenem administrativem Aufwand möglich.
Wir arbeiten mit Hochdruck daran, das Forum neu aufzusetzen und es sieht alles sehr vielversprechend aus.
Sobald es dies bezüglich Neuigkeiten, respektive einen Zeitplan gibt, lasse ich es Euch hier wissen.
Das wird auch für alle hier schon registrierten User wichtig sein, weil wir dann mit Euch den Umzug auf das neue Forum abstimmen werden.
Wir freuen uns sehr, wenn sich die geneigten Mitleserinnen und Mitleser, die sich bisher vergeblich um eine Freischaltung bemüht haben, nach der Neuaufsetzung abermals ein Herz fassen wollen und wir sie dann im neuen Forum willkommen heißen können.
Herzliche Grüße von Eurem ersten Vorsitzenden der IGDH
Rainer Feile
-
Chef Benutzer
Hörner aus Epoxy gießen
Moin miteinander,
ich möchte es nun langsam mal angehen, die Hörner, die ich im Constant Directivity thred berechnet habe, auch mal ins echte Leben zu holen. Dafür möchte ich mich mit dem gießen aus Epoxy auseinander setzen. Der Plan für das Horn sieht dabi erstmal so aus:
-->Gussform als 3D Druck
Ich hab in der Firma zugriff auf einen recht guten 3D Drucker. Damit möchte ich eine Schalung 3D drucken und diese dann ausgießen
-->Materialmix
Epoxy ist als Material schon recht gut geeignet denk ich(hohe Dämpfung und wenig flexiebel), aber da geht noch mehr. Im Hobby CNC Beerich ist Epoxy Granit ein Weg, einen Maschienenbasis mit hoher Dämpfung und hoher Festigkeit zu fertign. Diesen Weg möcht ich auch gehen, oder zumindest da starten.
Bevor ich mir den Aufwand mache, wollt ich ein Versuchsreihe zu möglichn Materialmixen starten. Sooo aufwendig wie es z.B. für die Epoxy Granit Mixturen gemacht wurde, will ich es aber garnicht machen. Die Idee ist folgend:
-->Testplatten aus den Materialmixien mit ca. 20x20x2 cm
-->Diese werden frei schwingend aufghangen z.B. an einem Draht
-->Ein Pendel mit einer Kugl am End wird zur Anregung verwendet und schwingt gegn die zu testende Platte(Ich meine, dass war mal von den ARTA Machern ein vorgeschlagner Test dazu, aber ich kann dazu leider nichts mehr finden).
--> Hinter der Platte steht ein Mikro und nimmt den entstehenden Schall auf.
Je höher die Dämpfung, desto weniger sollte das Mikro aufzeichnen. Ausschwingverhalten etc. könnte man dann auch bewerten.
-->Möglich Materialmixturen
Hir wird es spannend. Erstmal zum Hartz. Hier wollte ich eins nehmn, dass normalerweise für sogenannt infusions genommen wird. Dies zeichnet sich durch eine sehr gringe Viskosität aus und fießt noch zwischen auch sehr feine Granulate wie Sand. Im DIY Audio Forum hatt das schon jemand ausprobiert und gute Ergebnisse erzielt. Das Harz war das hier: https://www.easycomposites.eu/in2-epoxy-infusion-resin . Als Füllmatrial wollte ich hier mal anfragen: https://www.genan.de/produkte/gummipulver/ ob die auch kleine Mengen an Privatleute verticken. Dann könnt man mit Körnungen spielen und mir gefällt der Recycling Aspect dadran. Sand steht natürlich auch auf der Liste. Am Ende hätte ich gerne 5-6 verschiden Mixturen. Villeicht auch noch eine Platte mit Honeycombeinsatz um zu sehn, ob sich sowas als Gehäusematrial eignet.
Ich bin mir auch bewusst, dass der Aufwand durchaus in keinem Verhältnis stehen kann am Ende. Aber ich hab Bock auf das Thema =)
Was meint ihr zu der Testmethode? Sinnvoll so oder nicht? Hat einer von euch schon mal mit Harzen in der Richtung gearbeitet?
Meine Nachbarn hören auch Metal, ob sie wollen, oder nicht \m/
-
Gleich mal zu Anfang, sorry. Je nachdem wird Epoxy bei der Reaktion sehr, sehr heiß. Also darauf achten, dass das Filament das ab kann.
Gruß
Arnim
Das Universum schuldet einem nichts.
-
Chef Benutzer
Alles gut, wegen sowas frag ich hier ja =) Ich wollt die langsam härtende Variante nehmen um die Hitzebildung gering zu halten. Ist sonst weniger Härter zu nehmn eine Alternative?
Meine Nachbarn hören auch Metal, ob sie wollen, oder nicht \m/
-
Nein, das Harz muß im richtigen Verhältnis gemischt werden. Man kann Quarzsand hinzufügen. Muss man vorher testen. Selbstverständlich gibt es langsam härtendes Epoxy.
Edit: Mal hier anrufen: https://www.r-g.de/list/Harze/Epoxidharz
Gruß
Arnim
Das Universum schuldet einem nichts.
-
Erfahrener Benutzer
Geändert von 4711Catweasle (26.02.2024 um 19:07 Uhr)
Gruß Karsten
Wer den Blick immer nur stramm auf den Horizont gerichtet hat, stürzt über die Ruinen der Vergangenheit.
-
Warum nicht gleich ein Resindruck und anschließend lackieren?
Beim selbergießen sollte schon etwas Erfahrung vorhanden sein,
oder das gleich Lehrgeld mit einrechnen.
Gruß
Bernd
-
 Zitat von 4711Catweasle
Moin,
ich habe die Erfahrung gemacht das es Vorteile hat wenn die Gussform elastisch ist -> ausformen des Gießlings.
Über Positiv-Form, mit 2K Gießsilikon abgeformt, gibt es eine schöne Guss Negativform die mEn. sehr gute Guss Ergebnisse bringt.
Zudem (auch von der gegossenen Schichtdicke abhängig) solltest Du die eventuelle thermische Reaktion des Harzes beim Aushärten im Auge haben.
Trennmittel sind (falls notwendig) auch etwas tricky.....da mußte ich Lehrgeld zahlen.
Zur Testmethode fällt mir mangels Erfahrung nichts ein.....
Falls Du Fragen zu Formen / gießen hast gern - habe damals mit weißem Künstlerbeton und mit glasklarem Kunstharz (experimentell) gegossen.
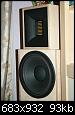
Cooles Ergebnis! Ich kapiere es noch nicht. Du hast eine negative Form aus Styropor gemacht und mit Sandpapier bekleibt? Wie hast Du denn das Profil reinbekommen? Zwei Schablonen und Heißdrahtschneider? Und dann kannst Du doch direkt von der Styroporform gießen, ohne Umweg über Silikon?
-
Erfahrener Benutzer
Geändert von 4711Catweasle (26.02.2024 um 20:55 Uhr)
Gruß Karsten
Wer den Blick immer nur stramm auf den Horizont gerichtet hat, stürzt über die Ruinen der Vergangenheit.
-
Vollaktiv per DSP
Beim Gießen von Epoxi sollte man auch das Schwundverhalten beim Aushärten im Auge behalten. Je mehr Füllstoffe (Epoxigranit, Quarzsand) desto weniger Schwund. In den technischen Datenblättern steht so etwas in der Regel drin. Wenn nicht sollte das Harz wohl eher nicht für Formguss verwendet werden.
Gruß, Onno
wissen ist macht. nicht wissen macht auch nichts.
-
Hallo,
30% Basaltsplitt 2-4 mm (links), 30% Fugensand 0-2 mm (mitte), 30% Quartzsand 0,1-0,4 mm (rechts) und 10% Epoxyharz L und Härter L von (Werbung ein )R&G.DE
Das Ganze bei 70- 80° tempern.
Wenn du dem noch eins draufsetzen willst dann im Vakuumbag.
Eine Gummi-Harz matrix kannich mir nicht gut vorstellen., Dazu ist das Harz zu spröde. Dazu brächte es ein Schichtenaufbau.
-
HSG Bayern
Hmm, also akustisch tot solls werden,,, Da würde ich auf jeden Fall auch mal diverse Härten testen,, Das geht mit Zusatz von einem Flexibilisator,,, Die Testplatten würde ich nur 1cm dick machen .....
LG, Manfred
-
Hallo.
Schließe mich den Vorrednern an.
Mischung mit Gummigranulat rate ich von ab.
Polymerbeton/Mineralguss kann man sehr gut die o.g. Mischung nutzen. Das funktioniert gut.
Exothermie ist bei solchen Mischungen nicht so wild. Die 90% mineralischer Zuschlag sind ein guter "thermischer Sumpf" für die 10% epoxy.
Die Gesamtmasse überschreiten während der Reaktion nicht die kritischen Temperaturen. Für so viel kalte Masse reicht die frei werdende Energie nicht aus.
Statt Infusionsharz würde ich eher Richtung 30-45min Topfzeit gehen. Für das Infusionsharz muss die Schalung sehr dicht sein .
Das wird bei mir nicht zu heiẞ mit o.g. Mischung (Hörner und Plattenspieler gegossen damit u.a.)
Zum Formenbau und dem Thema Schwinden wurde viel gutes gesagt,unbedingt beachten.
Ich entnehme deinen Ausführungen, dass keine Erfahrungen mit epoxy und Guss vorhanden sind.
Daher auf jeden Fall Lehrgeld einkalkulieren.
Ich frickel seit fast 30 Jahren mit Epoxy rum und gieße fast so lange Teile aus epoxy oder uhpc Beton.
Hab Mal mehrere Sätze elliptische Hörner gegossen (45cm lang, Öffnung 50*70cm Ellipse).
Das war gut aus Mineralguss. Uhpc war aber nochmal hörbar besser (hatte identische Lautsprecher aufgebaut und nebeneinander aufgebaut und mit direkten umschalten gehört)
-
HSG Bayern
Ich hatte früher beruflich auch mit Epoxi Gießharzen zu tun.. Optimal fließende Massen bekommt man mit Glaskugeln als Füllstoff - war letzlich für die Serie zu teuer...
-
Ja, das funktioniert gut mit den Glaskugeln für die Erhöhung der Fließfähigkeit.
Das Fließen der Masse ist für die spätere Eigenschaft, die ich bei Guss-Hörnern anstreben würde aber kontraproduktiv.
Die Verzahnung der einzelnen Zuschlagstoffe und die Minimierung des Harzanteils ist ja das gute am Polymerbeton/Mineralguss
Man bekommt hobbymäßig weder die industrielle Sieblinie, noch den sehr geringen Harzanteil, noch den Verdichtungsgrad hin.
Für das was man erreichen will kommt man aber mit 10-15% Harzanteil und Verdichtung mittels an die Schalung gehaltenem Exzenterschleifer o.ä. zu sehr guten Ergebnissen.
-
Chef Benutzer
Hallöchen,
erstmal danke für den vielen Input! Das hilft mir ziemlich weiter, also schonmal dank dafür. Ich fasse die Punkte so weit mal zusammen:
-->Schrumpfung beachten
-->Temperatur beachten bei wenig Füllmaterial
-->Flexibilisator um Dämpfung zu erhöhen testen
-->Damit rechnen, das es schief geht, da keine erfahrung =)
@Rainer Dank für das Rezept! Aber was meinst du mit rechts/links/mitte?
@Bizarre Spannnds Mittel, hatte ich so auch noch nicht von gehört. 1 cm um erstmal Material zu sparen?
Dann mache ich mal meine Hausaufgaben =) Ich würde dennoch gerne Gummi versuchen. Es geht wie gesagt ja erstmal um einzeln Testplatten und ums kennen lernen des Materials. Da tut ein spröder Fehlversuch nicht weh find ich.
Meine Nachbarn hören auch Metal, ob sie wollen, oder nicht \m/
-
HSG Bayern
Den "Flexibilisator" hab ich erst gestern entdeckt... Wir hatten früher ein flexibles mineralgefülltes System für den Verguß unserer Sensoren... Einfach per Härterüberschuß flexibler machen geht wohl nur mit UHU endfest 300 ..
Jo, 2cm wären für mich "Materialverschwendung".... Lieber noch nen "regionalen" Füllstoff ausprobieren : Hartweizengries. Im Gegensatz zu Sand etc.ist Nacharbeit kein Problem.....
-
Chef Benutzer
Ok, dass Weizengris kommt mit auf die Liste. Genan hab ich bzgl. Samplemengen mal angeschriben und ein Silikonform von Amazon ist heut angekommn. Die Tage werd ich mich für ein Harz entscheiden und anfangen, die Proben die ich schon anfertigen kann zu gißen.
Meine Nachbarn hören auch Metal, ob sie wollen, oder nicht \m/
-
Denk beim Epoxy an ensprechende Belüftung - das Zeug ist nicht ohne und wenn du mal eine Alergie entwickelt hast bekommst du die auch nicht mehr so schnell los.
-
Hallo 3eepoint,
schön, dass jetzt die Praxis kommt - bin auf die Ergebnisse gespannt!
In kurz:
Ich habe ja schon einiges an Hörnern mit Epoxy gebaut. Epoxy ist ja auch das "gesunde" Harz - im Vgl. zu Polyesterharz ist aber trotzdem allergen. D.h. auf Arbeitsschutz in Form von Handschuhen, körperbedeckender Arbeitskleidung etc. ist zu achten. Außerdem schwindet Epoxy auch deutlich weniger.
Vom reinen Gießen wäre ich nicht überzeugt. Ich habe immer mit Glasgewebe (also Köper, welches kreuzweise gelegt wird um quasiisotropie zu erreichen) gearbeitet. Für die Erhöhung der Dicke bieten sich als "Füllung" Styrodurformteile an.
Vorteil: wesentlich größere Festigkeit und es reicht eine einseitige Form, also nur Negativform - was für die Hornkontur zu bevorzugen wäre - oder Positivform - dann eben mit Nachbearbeitung der Hornkontur durch schleifen.
Kleber: mit Baumwollflocken eingedicktes Harz
Spachtel: Glassbubbles ins Harz rühren
Eindicken um Abflißen zu verhindern: Aerosil.
Etwas ausführlicher:
Zunächst mal zum Formenbau:
Meine Empfehlung: Negativ-Bauweise. Das hat den Vorteil, dass Du nach dem Ausformen gleich eine brauchbare Oberfläche bekommst.
Die Oberfläche der Form sollte hart sein, damit Du nach dem Ausformen nicht zuviel nacharbeiten musst, v.a. wenn Du die Form wiederverwenden willst.
Bei der Gestaltung der Form der Form darauf achten, dass es sich ausformen lässt (mieser Ausdruck, ich weiß).
Die Oberfläche auf mindestens 800er Körnung schleifen (besser 1000er).
Beim Schleifen ist Geduld gefragt. Das dauert! Denk dran: Bei einer glatten Oberfläche ist nachher jede Delle zu sehen!
Wenn die Form fertig ist, kannst Du ans Laminieren denken. Als Trennmittel empfehle ich: PVA. Das lässt sich leichter ausformen als 'ne gewachste Form. Falls Du wachsen willst: Das Wachs dünn auftragen und nach Trocknung auspolieren. Aber nicht nur einmal, bei einer neuen Form eher so 15mal wiederholen.
Dann das Harz: Kein Polyesterharz verwenden (schwindet und stinkt)! Ich empfehle Epoxidharz. Schau Dich mal nach 'nem guten Harzsystem um, zu dem Du auch ein vernünftiges Datenblatt bekommst.
Härter: Da die Form wohl groß wird->langsamer Härter!
Anmischen mit Waage, je nach offener Zeit immer so 100g-weise.
Es gibt Färbemittel für Harze, damit sparst Du Dir (wenn Du sauber arbeitest) die Lackierei.
Wenns jetzt losgehen soll, zunächst mal Latexhandschuhe anziehen (Epoxi kann Allergien auslösen).
Die Form schön mit Harz einpinseln, dann die erste Lage rauf.
Als Gewebe würde ich Köper nehmen, das lässt sich in alle Richtungen beliebig legen (im Ggs. zu UD, das geht nur in eine Richtung). Hast Du scharfe Umlegestellen, dann legst Du zuerst eine Lage feines Gewebe (z.B. 80g/m²). Schön festtupfen, dabei immer ein wenig Harz auf dem Pinsel haben, aber nicht mit Harz übertreiben, auch wenn's leichter geht. Achte darauf, dass sich keine Luftblasen bilden!
Anschließend schmierst Du auf die scharfen Kanten Mumpe, so wird in "Fachkreisen" eingedicktes Harz genannt, also ein harzbasierter Spachtel. Als Füllmaterial (zum Eindicken) kannst Du Baumwollflocken nehmen.
Wenn das erledigt ist, dann eine Lage dickeres Gewebe (z.B. 163g/m² oder mehr) und evtl. noch 'ne Lage. Die einzelnen Lagen immer schön festtupfen und keine Luftblasen drinlassen (sonst Delamination->kaputt).
Damit das Horn auch steif wird (und Du nicht soviel Gewebe brauchst), kannst Du jetzt Schaum aufkleben. Also Styrodur in Form schneiden und mit Mumpe aufkleben anschließend noch 'ne Lage Gewebe.
Wenns ganz toll werden soll, dann lässt Du das Zeug mit Absaugung aushärten. Ich denke jedoch, dass Du die dafür nötige Vakuumpumpe nicht haben wirst.
Du kannst auf die letzte Gewebelage noch Abreißgewebe legen, das gibt 'ne tolle, saubere Oberfläche auf die Du evtl. gleich wieder drauflaminieren kannst.
Dann alles Aushärten lassen (Zeit ist abhängig vom Harzsystem) und anschließend idealerweise Tempern.
Das Tempern dient dazu, dass das Laminat auch bei höheren Temperaturen nicht seine Form verliert.
Dazu aus Styroporplatten ein "Temperzelt" basteln. Auf einer Seite mit'm Heizlüfter reinpusten und die warme Luft auf der anderen Seite wieder rauslassen. Das Laminat ist natürlich auf der Form. Dann das Ganze ca. 15h auf 75°C halten.
Dabei wird das Harz wieder weich und härtet nach Abkühlung wieder aus und bleibt auch bei höheren Temperaturen fest.
Wegen Temperzeit und -Temperatur ins Datenblatt schauen.
Viele Grüße
André
-
HSG Bayern
Forumregeln
- Es ist dir nicht erlaubt, neue Themen zu verfassen.
- Es ist dir nicht erlaubt, auf Beiträge zu antworten.
- Es ist dir nicht erlaubt, Anhänge hochzuladen.
- Es ist dir nicht erlaubt, deine Beiträge zu bearbeiten.
-
Foren-Regeln
|